Papers
Our papers
We gladly share our expertise and experience with anyone interested in the fields of hydrodynamics and computational fluid dynamics (CFD).
Our papers are freely available for download – subject to copyright restrictions, of course!
Hull Vane® vs lengthening – a comparison between four alternatives for a 61m OPV
Can you achieve the same performance by lengthening a ship as with a Hull Vane? This case study finds out for a 61m offshore patrol vessel from Damen Shipyards, and looks at the performance of both the appended and integrated Hull Vane. This paper was presented at the FAST conference in 2017.
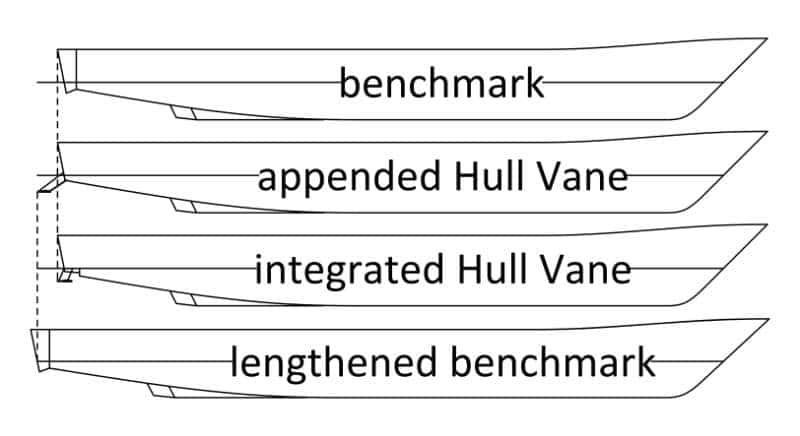
Hull Vane® on 108m Holland Class OPV: effects on fuel consumption and seakeeping
This paper describes the CFD work done in both calm water and waves for the 108m Holland Class Offshore Patrol Vessel, highlighting a.o. the positive effect on helicopter landings. This paper was first presented at the MAST conference in 2016.
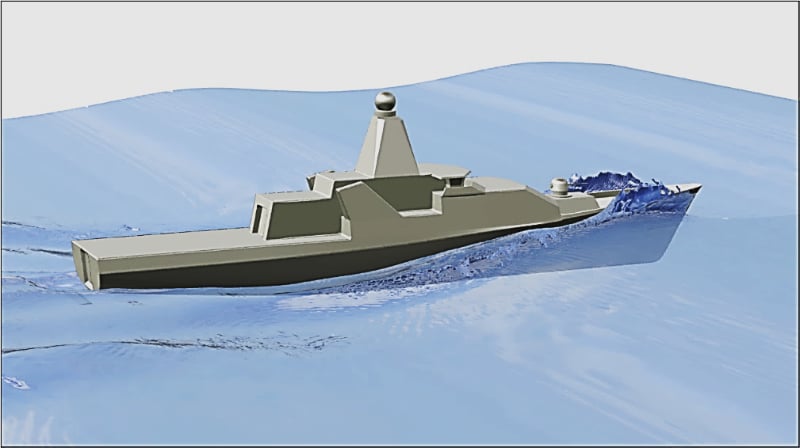
A systematic comparison of the influence of the Hull Vane®, interceptors, trim wedges, and ballasting on the performance of the 50m AMECRC series #13 patrol Vessel
How does Hull Vane® compare with interceptors, trim wedges, and ballasting. Which performs best at which speed? This paper compares various stern devices on a typical publicly available round-bilge fast-displacement hull, often used as parent hull for OPV and superyacht designs. This paper was presented at the RINA Warship Conference in Bath, UK, in 2016.
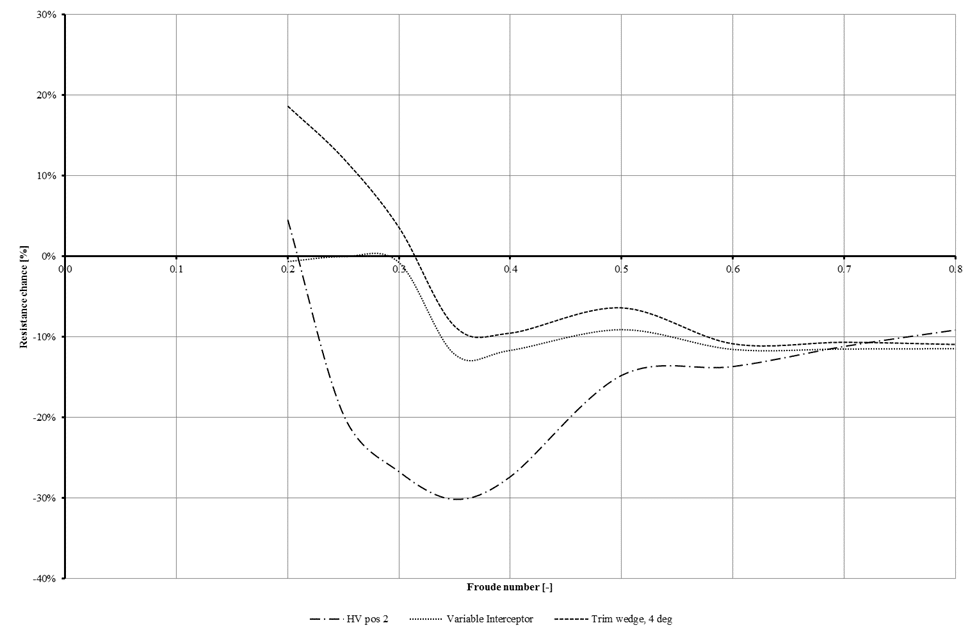
A life cycle cost analysis of the application of a Hull Vane® to an offshore patrol vessel
A Hull Vane® was optimised for the Holland Class 108m Ocean-going Patrol vessel of the Royal Netherlands Navy, and its effects were studied by means of a Computational Fluid Dynamics study. This paper demonstrates that the total fuel consumption can be reduced by around 13% if a Hull Vane® is installed. A method for evaluating energy saving devices on ships with a wide operating profiles is used.
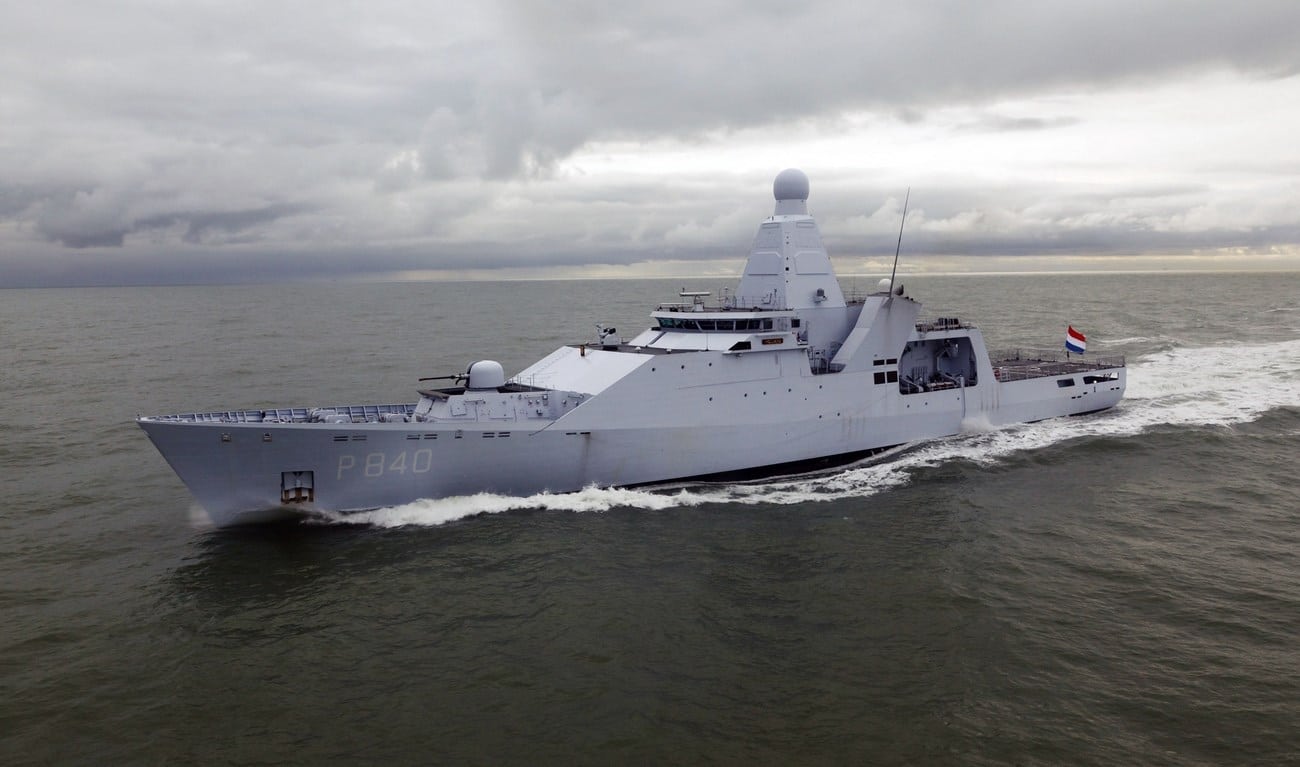
The effects of the Hull Vane® on ship motions of ferries and RoPax vessels
This paper discusses research into the resistance and seakeeping aspects of the Hull Vane® on larger vessels. Results from tank tests of the 167m container ship Rijnborg and CFD computations on the 167m RoPax vessel Norbank are discussed. These results show that the resistance, the pitch motion and the added resistance due to waves can be effectively reduced by applying a Hull Vane® on larger vessels operating in the Froude range 0.20 to 0.30.

An underwater spoiler on a warship: why, when and how?
This paper gives an overview of several studies which have been done on naval and coastguard ships. The paper gives insight in the concrete capability improvements for such ships through relevant case studies. The paper was presented at the 8th International Science and Technology Conference for Naval Technologies for Defence and Security, in June 2018 in Gdansk, Poland.
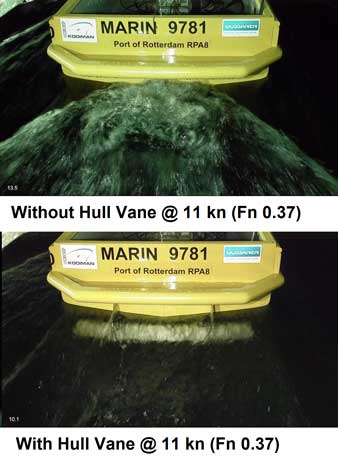
Improving the nautical performance of a surface ship with the Hull Vane® appendage
Extract from ATMA bulletin n°118. This paper shows the results of a study done by Naval Group on a naval surface ship, comparing an optimized trim wedge, interceptor and stern flap with an optimized Hull Vane®. The results of CFD analyses are presented, as well as model test results, carried out at MARIN, including seakeeping tests, maneuvering trials and cavitation tests. Significant gains on resistance and propulsive power were obtained, and exceeded largely what is obtained with more classic stern appendages.
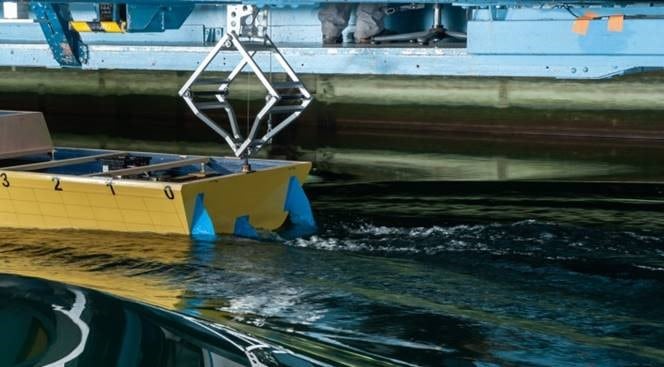
Enhanced Dampening of the Pitch Motions with an Actively Controlled Hull Vane
Among other characteristics, a main performance parameter of a yacht is comfort. The parameter is dominated by ship motions. Besides a well-designed hull, several appendages can be used to increase performance. One of these is the Hull Vane®, a patented energy-saving and seakeeping device which consists of a submerged wing mounted on the aft ship. The Hull Vane® is an appendage with the potential to create large lift forces on the aft of the ship, thereby changing the resistance and dynamic position of the vessel.
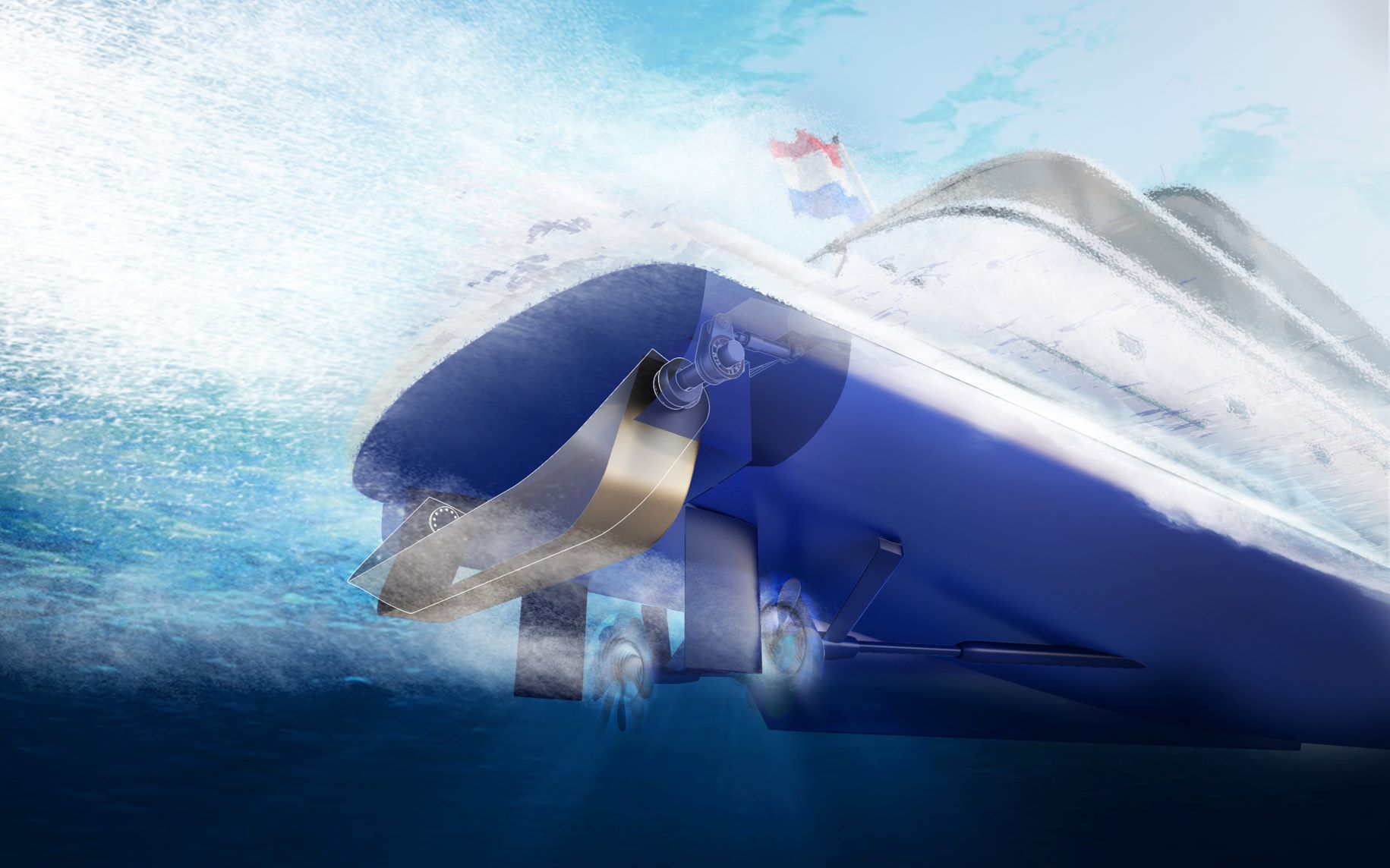